At Fullscript, your health and safety are a top priority. Each brand and product offered in Fullscript’s catalog must meet strict quality standards, which provide you with peace of mind when selecting supplements. With so many options available, it can be challenging to choose the ideal natural health products for you or your patients. Fullscript makes it easy to access the information you need regarding supplement quality by providing transparency regarding all of the brands offered in the catalog. Continue reading to learn more about Fullscript’s vetting process, quality standards, and dietary supplement quality assurance.
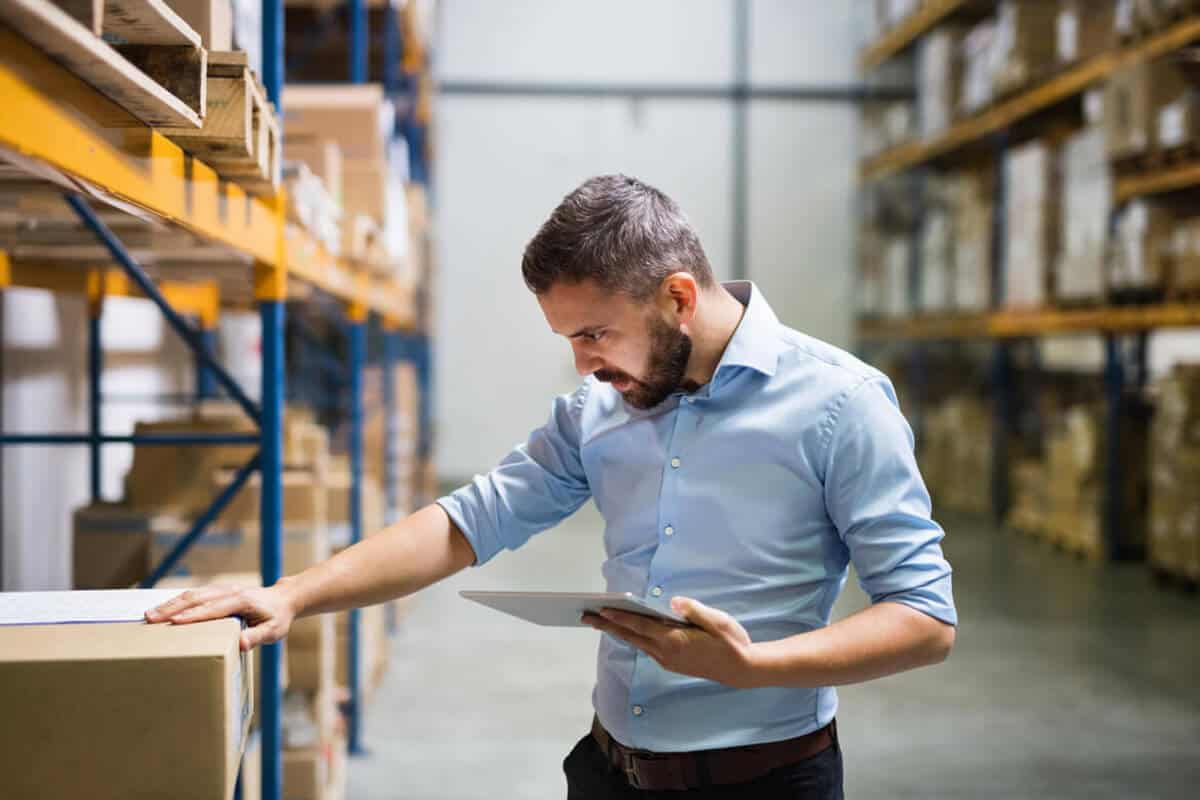
Ready to start delivering better patient care?
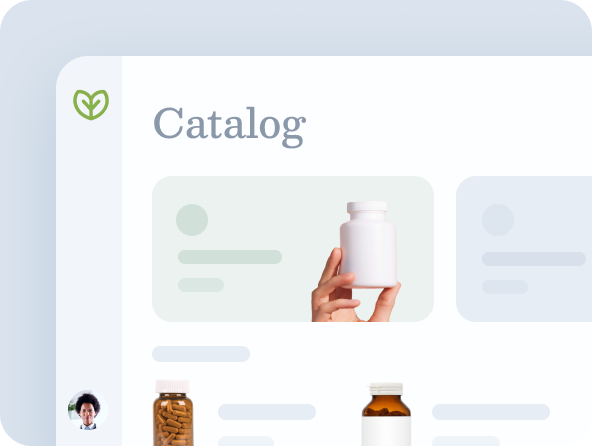
Why is supplement quality important?
The Food and Drug Administration (FDA) and Health Canada are the government organizations that oversee the regulation of dietary supplements and natural health products in the United States and Canada, respectively. (1)(4) However, dietary supplements are not as strictly regulated as pharmaceutical medications, and many supplements lack transparency regarding purity, quality, and safety.
If the production and distribution of a product do not adhere to strict manufacturing standards, often reviewed by a third-party certifier, the product may include incorrect or adulterated ingredients, display inaccurate labels, and risk cross-contamination with other ingredients or microbiological contamination, among other critical issues that may affect product quality, and ultimately, consumer health. (4)
When considering supplement quality and safety, many dietary supplement manufacturers assess products using a set of standards known as Good Manufacturing Practices (GMPs). These standards help ensure the identity, purity, strength, and composition of the products that are being manufactured. (4)
Did you know? In the U.S., the FDA regulates dietary supplements under a set of framework established by the Dietary Supplement Health and Education Act of 1994 (DSHEA). (11)
Good Manufacturing Practices (GMPs)
Good Manufacturing Practices are standards implemented by the FDA and developed with the intent to protect consumers and allow all supplement manufacturers and resellers of supplements to eliminate the presence of unsafe and incorrect ingredients in their products. The GMP standards also ensure that products are labeled and packaged accurately, and are produced without contamination. (4) These standards allow distributors, like Fullscript, to be held accountable for consumer safety and ensure their products meet quality standards.
Good Manufacturing Practice (GMP) is sometimes referred to as Current Good Manufacturing Practices (cGMP). (2) The Current Good Manufacturing Practices serve as a guideline to supplement manufacturers and distributors to maintain up to date equipment, technologies, manufacturing processes, and policies. (2)
cGMPs exist to help ensure that supplements are produced consistently and meet specific quality and safety standards. (11) To be cGMP-certified, manufacturers must adhere to the following standards:
- Places – locations where products are manufactured and stored are sanitary
- People – employees are trained on proper cleanliness and safety processes
- Processes – consistent operations are in place to provide authenticity and safety
- Products – products are checked throughout manufacturing, storage, and delivery for authenticity, safety, and accuracy
Adding new brands at Fullscript
To ensure the catalog provides the highest quality products to practitioners and patients, Fullscript partners with the top professional-grade brands that are compliant with cGMP standards. All brands available in the Fullscript catalog undergo a thorough vetting process, so you can be sure that all products offered are manufactured with safety and quality in mind.
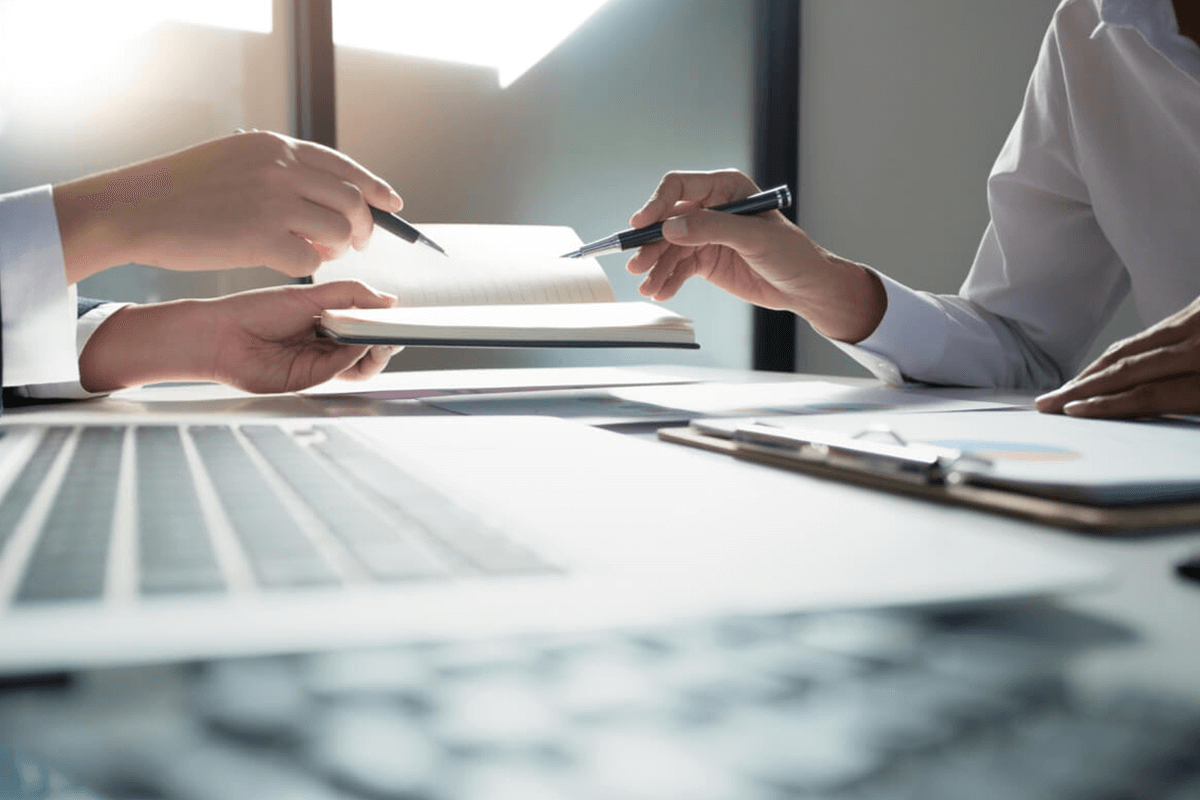
Fullscript maintains the most comprehensive catalog in the industry and works to ensure that all brands meet strict policy and manufacturing standards before any brand or product is added to the catalog. The process for bringing on new brands involves an in-depth supplement quality control questionnaire that requires the disclosure of the following information from brands:
- cGMP auditing & certifications
- Compliance reporting
- Description of internal quality teams
- FDA inspections
- Finished goods quality testing practices
- Internal training programs on quality maintenance
- Label and facility testing
- Manufacturing personal information (both internal and external)
- Quality assurance policies and processes
- Raw ingredient information
- Recall procedures
- Testing for adulterants and contaminants (e.g., heavy metals, chemical substances, pesticides)
In collaboration with Fullscript’s Medical Advisory Team, the Quality Assurance team has established the Fullscript Quality Assessment, a comprehensive evaluation that allows brands to identify any measure taken that exceeds the basic quality standard requirements. This process not only applies to new brands, but existing brands as well. Fullscript also strongly encourages current brands to register with third-party certification programs to further establish themselves as reputable supplement brands and to demonstrate their commitment to produce high-quality and safe products. Examples of common third-party certifications include the following:
- International Organization for Standardization (ISO) 9001 (3)
- NSF International (6)
- Non-GMO Project (8)
- Natural Products Association (NPA) (5)
- SGS (General Society of Surveillance) (7)
- Underwriter Laboratories (UL) (9)
- USDA Organic (10)
- USP
Storage of dietary supplements at Fullscript’s distribution centers
Fullscript’s distribution centers operate according to cGMP standards and in compliance with the NSF International guidelines. Careful considerations are made regarding proper supplement storage, transport, and delivery to ensure each product is maintained and handled according to the manufacturer’s instructions. Proper storage is particularly important for dietary supplement products, as many require storage in specific temperatures to prevent ingredient degradation and spoilage.
Similar to manufacturer requirements, Fullscript’s distribution centers adhere to cGMP standards for the storage of supplements, including attentiveness to cleanliness, ensuring employee safety training, and having consistent operation processes in place.
All of Fullscript’s distribution centers adhere to safety codes and follow manufacturer standards for proper storage. Shelf-stable products are stored in a temperature-controlled environment maintained at a temperature of 68 to 77 degrees Fahrenheit (18 to 25 degrees Celsius). Heat-sensitive products, such as certain probiotics and omega-3 fatty acids, are stored in refrigerated environments at 36 to 46 degrees Fahrenheit (2 to 7 degrees Celsius), with humidity at no more than 60%. Temperatures are monitored 24/7, 365 days a year to guarantee that the products are continuously stored at their recommended temperatures.
Furthermore, all facilities are regularly inspected for sanitation standards, personal hygiene compliance, pest control, and equipment maintenance.
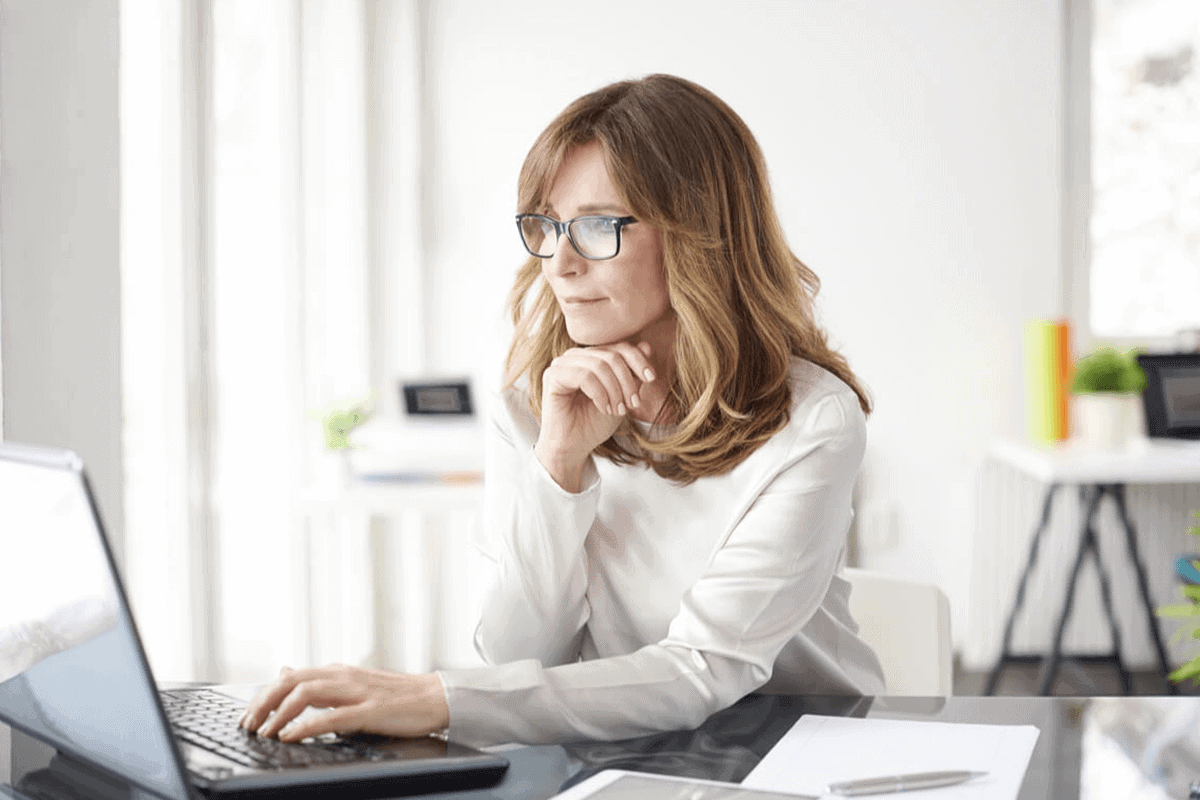
Product recall process
Fullscript has a dedicated team responsible for overseeing product recalls and monitoring any quality concerns initiated by consumers and manufacturers. Although uncommon, supplement recalls can happen. Fullscript works closely with manufacturers and brands, allowing for a quick response in the event of a product recall.
Once alerted of a product recall, Fullscript quarantines existing products in affected distribution centers and notifies practitioners directly. Practitioners of patients who have purchased recalled products are urged to advise their patients immediately. Provided in the communications to practitioners are clear instructions for handling the return or disposal of affected products.
Product complaint process
In the event of a quality concern or product complaint from a practitioner or patient, Fullscript maintains a rigorous quality consumer complaint procedure. When a consumer contacts Fullscript’s Customer Success team with a product complaint, all pertinent details are recorded, including lot numbers and expiration dates, and the complaint is reported internally, as well as to the specific brand.
Complaints help the Quality Assurance team forecast possible voluntary recalls from brands, and they also allow Fullscript to continually evaluate the quality of the brands in the catalog. Depending on the nature of the complaint, Fullscript may request that the product be returned so that the brand can conduct necessary quality testing.
Direct shipments to patients
Once an order is placed, items are carefully packaged and shipped promptly to patients. Fragile products, such as supplements in glass bottles, are packaged with extra care to prevent damage while in transit.
Most heat sensitive-products are shipped inside an insulated pouch containing a reusable cold pack to keep them cool in transit. The fully frozen cold pack is placed into the insulated pouch when the order is prepared to ship, and as the cold pack thaws over the following days, the insulated pouch continues to keep the product cool. Heat sensitive products are designed to withstand short-term temperature variations, and remain safe and effective to use. If indicated on the product’s label, be sure to promptly place the product into the refrigerator for long-term storage.
Did you know? Fullscript has five distribution centers in the U.S., located in Arizona, Pennsylvania, California, Kansas, Virginia, as well as a distribution center in Ontario, Canada.
The bottom line
At Fullscript, product safety and quality are a top priority. When introducing a new brand, the Fullscript Quality Assurance team carefully reviews all products, including their standards, certifications, any associated complaints, claims, compliance with FDA guidelines, and more. Fullscript stands apart from many retailers who do not specialize in supplements and, therefore, may not have the same measures in place to ensure product quality and handle product recalls. Fullscript’s priority is to offer products that have been meticulously selected and monitored, stored, and shipped with care.
Ready to start delivering better patient care?
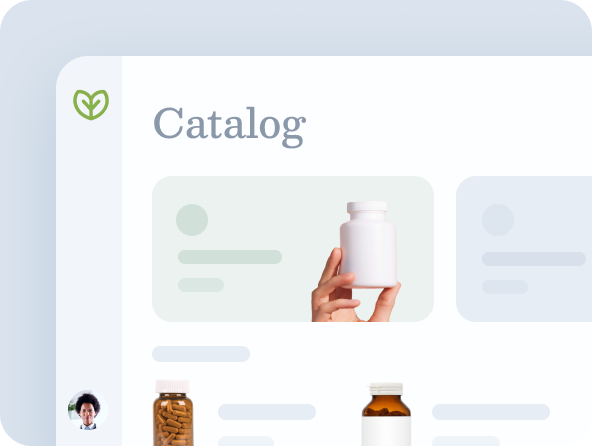
- Health Canada. (2020). Natural and non-prescription health products directorate. https://www.canada.ca/en/health-canada/corporate/about-health-canada/branches-agencies/health-products-food-branch/natural-non-prescription-health-products-directorate.html
- International Society for Pharmaceutical Engineering. (n.d.). What is GMP? https://ispe.org/initiatives/regulatory-resources/gmp/what-is-gmp
- ISO. (2020, June 11). ISO 9000 family — Quality management. https://www.iso.org/iso-9001-quality-management.html
- National Institutes of Health. (2020). Dietary supplements: What you need to know. https://ods.od.nih.gov/factsheets/WYNTK-Consumer/
- Natural Products Association. (n.d.). Natural Products Association. https://www.npanational.org/
- NSF. (2021, February 24). Food consulting solutions. NSF International. https://www.nsf.org/consulting/food
- SGS. (n.d.). SGS. https://www.sgsgroup.us.com/
- S.784 – Dietary Supplement Health and Education Act of 1994 (n.d.). https://www.congress.gov/bill/103rd-congress/senate-bill/784/text
- The Non-GMO Project. (n.d.). What is a GMO? – the Non-GMO Project. Non-GMO Project. https://www.nongmoproject.org/gmo-facts/what-is-gmo/
- UL. (n.d.). UL Empowering Trust. https://www.ul.com/
- U.S. Department of Agriculture. (n.d.). USDA Organic. https://www.usda.gov/topics/organic
- U.S. FDA. (2007, June 25). Current good manufacturing practice in manufacturing, packaging, labeling, or holding operations for dietary supplements. https://www.federalregister.gov/documents/2007/06/25/07-3039/current-good-manufacturing-practice-in-manufacturing-packaging-labeling-or-holding-operations-for
- U.S. FDA. (2020, September 21). Current good manufacturing practice (CGMP) regulations. https://www.fda.gov/drugs/pharmaceutical-quality-resources/current-good-manufacturing-practice-cgmp-regulations
- US Pharmacopeia (USP) | USP. (n.d.). https://www.usp.org/